Диспетчеризация производства
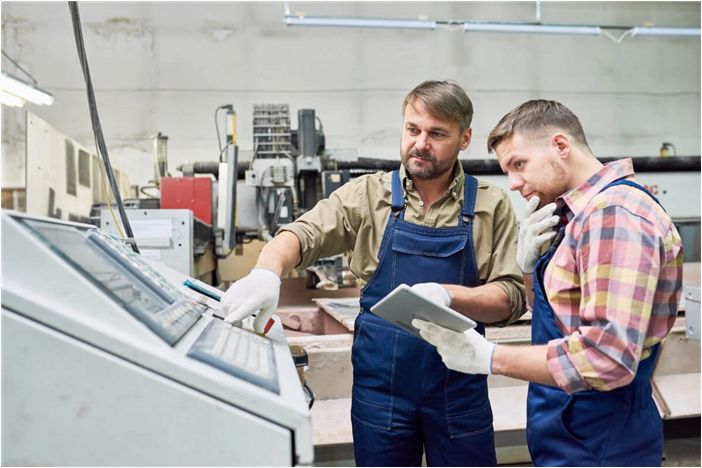
Диспетчеризация производственных процессов — одна из самых актуальных проблем для современных компаний, поскольку от того, как организованы и спланированы рабочие процессы в цехе, зависит эффективность всего производства. Для ее решения необходимо внедрение автоматизированных систем, позволяющих быстро, точно и адекватно оценивать и анализировать текущую ситуацию и принимать рациональные и своевременные управленческие решения.
Содержание статьи:
Диспетчеризация как процесс управления
Существуют схемы разделения структуры производственного предприятия на стратегический, тактический и оперативный уровни управления. Диспетчерская служба относится к оперативному уровню управления и имеет дело только с производственной информацией.
До недавнего времени диспетчеризация осуществлялась либо вручную диспетчерской службой, либо с помощью системы, где работа основывалась на знании процессов, которые выполнялись в прошлом. В обоих случаях было сложно оценить текущее состояние производственной системы и спрогнозировать возможные сбои.
На смену устаревшим подходам к управлению производственными процессами пришли автоматизированные информационно-вычислительные системы. Это повышает эффективность диспетчеризации благодаря возможности отслеживать условия в режиме реального времени, изменять график операций с учетом неожиданных изменений в расписании и составлять точные прогнозы.
Системы диспетчеризации значительно упрощают администрирование, экономят рабочее время сотрудников и устраняют ошибки в принятии решений, вызванные человеческим фактором.
Цели диспетчеризации
Диспетчерское управление является заключительным этапом оперативно-производственного планирования и обеспечивает непрерывный систематический контроль за выполнением планов и графиков, касающихся изготовления продукции, координацию работы взаимосвязанных производственных звеньев (цехов, участков, рабочих мест) и устранение последствий, возникающих при отклонении от установленного графика работы.
Целью диспетчерского контроля является выполнение плановых заданий, подготовленных на этапе планирования производства. При этом работа должна быть организована таким образом, чтобы обеспечить максимально эффективное использование всех ресурсов, связанных с производством продукции, соблюдение сроков выполнения заказов и получение продукции надлежащего качества. Выход.
Эти цели могут быть достигнуты при определенных условиях.
- Взаимосвязанный график работ для всех подразделений, который устанавливает наличие, задачи и производственные курсы жизнеспособной и разумной производственной программы, позволяет сравнивать с фактической ситуацией и выявлять отклонения;
- Обеспечивает все подразделения предприятия необходимыми ресурсами. Техническая документация, сырье, материалы, инструменты и т.д;
- Использование процессного управления, которое обеспечивает гибкий подход к имеющимся ресурсам, предоставляет возможность перераспределения для предотвращения отклонений;
- Возможность оперативной координации графиков и задач в процессе производства продукта.
Эти условия могут быть соблюдены с помощью систем MES. Это инструмент для автоматизации планирования и диспетчеризации производства.
Задачи и функции диспетчеризации
Основными задачами диспетчера являются:
- Контроль и координация производственного процесса;
- Обеспечение равномерной загрузки оборудования;
- Поддерживать непрерывность, ритмичность и эффективность всех процессов;
- Предотвращение простоев оборудования и потерь рабочего времени.
Производство — это живой организм, в котором происходит множество процессов, изменения происходят одновременно и постоянно случаются неожиданности. Задача диспетчерской службы — тщательно следить за всеми процессами, немедленно реагировать на неполадки и постоянно искать пути совершенствования.
Функции системы диспетчеризации включают:
- Глобальный мониторинг состояния цеха, отдельного участка и рабочего места в режиме реального времени;
- Сбор и обработка исходных данных с более высоких уровней управления предприятием;
- Планирование и учет операций по перемещению сырья и полуфабрикатов;
- Перераспределение материальных потоков в зависимости от изменения условий производства;
- Оперативное управление запасами и производственными ресурсами;
- Управление соблюдением норм технического регулирования;
- Мониторинг и прогнозирование фактического состояния технического оборудования;
- Мониторинг и контроль качества;
- Прогнозирование и предупреждение неисправностей, отказов и аварийных ситуаций;
- Формирование диспетчерских отчетов о состоянии производственных процессов и выполнение планов.
Диспетчеризация в СНАРЯД | MES
Shell|MES — это система оперативного управления, которая позволяет оптимизировать производство, сделать его более гибким и эффективным за счет быстрого реагирования на события. Она включает в себя два уровня внутреннего краткосрочного планирования и диспетчеризации.
Система выигрывает от использования методов искусственного интеллекта и нового класса алгоритмов — мультиагентных вычислений. Ее реализация обеспечивает:
- Достижение максимальной прозрачности каждого процесса, происходящего в цехе;
- Возможность управления в зависимости от текущей ситуации;
- Понимание актуальных изменений во всей логистической системе предприятия;
- Внедрение наиболее эффективных на данный момент способов организации работы;
- Возможность немедленной оценки имеющихся ресурсов.
Создание единого информационного пространства для пусковых установок промышленного предприятия|MES может быть интегрирована с другими программными продуктами диспетчерских систем APS, ERP и АИС.