Порошковые лакокрасочные материалы
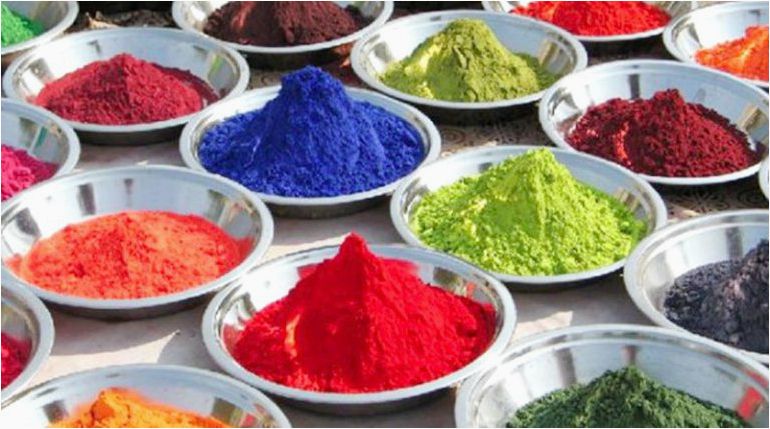
Порошковое окрашивание — это безотходная и экологически чистая технология получения полимерных покрытий с улучшенными защитными и декоративными свойствами. Порошковая технология была разработана и начала использоваться в 50-х и 60-х годах прошлого века. Сегодня около 15% мировой лакокрасочной продукции — это обработанные порошковые краски. Перед тем как порошковая краска купить следует ознакомится различными свойствами этого материала.
Содержание статьи:
Основное отличие обычных жидких материалов от технологии нанесения порошковых материалов заключается в том, что порошковые краски не содержат исходного жидкого растворителя и изначально находятся в твердом агрегатном состоянии.
Порошковые краски представляют собой смеси органических пленочных форм пигментов, наполнителей, сухих олигомеров или полимеров, которые растворяются, образуя непрерывное пленочное покрытие. В состав порошковых материалов входят следующие компоненты:
- Образование пленки — термопластичные полимеры или термореактивные олигомеры;
- Пигменты и наполнители;
- Модификаторы;
- Стабилизаторы;
- Структурирование веществ.
В зависимости от типа пленки, ранее входившей в состав порошковых красок и лаков, последние делятся на эпоксидные, эпоксидно-полиэфирные, полиэфирные, полиуретановые, полиакриловые, полиэтиленовые, полиамидные и т.д. и конкретные области применения.
Частицы пигмента в несколько раз более инертны, чем частицы полимера, не повышают температуру плавления и вязкость расплава. Также не замедляйте образование пленки. Для пигментации используются высокодисперсные, скрытые и термостойкие пигменты: диоксид титана, диоксид титана, железокислородные пигменты, технический углерод, фталоцианиновые пигменты. Также наполнители — тальк, барит и аэросил.
Независимо от состава, порошковый материал представляет собой однородный, невозбужденный сыпучий порошок с зернами размером 10-100 мкм.
Технология производства порошковых ЛКМ
Для получения цвета порошка используются три различных метода:
- Сухое смешивание дисперсных компонентов;
- Смешивание и последующее измельчение во время плавления;
- Диспергирование пигмента в растворе для пленочного слоя с последующим споротом растворителя из жидкого материала.
Сухие смеси используются для пигментации предварительно измельченных термопластичных полимеров. При использовании этого метода нерасширяющиеся стабильные композиции могут быть получены только в том случае, если при смешивании между частицами исходного материала и гетерогенными частицами происходит образование новых смесительных узлов с большой поверхностью контакта. При сухом смешивании без измельчения полимерных частиц частицы пигмента и наполнителя «обнажают» поверхность полимерных зерен снаружи. Полярные полимеры (например, поливинилбутираль, полиамид, эфир целлюлозы) обладают хорошей адгезией к дисперсным пигментам и наполнителям. Неполярные полимеры (например, полиолефины, фторопласты) гораздо труднее смешивать с наполнителями.
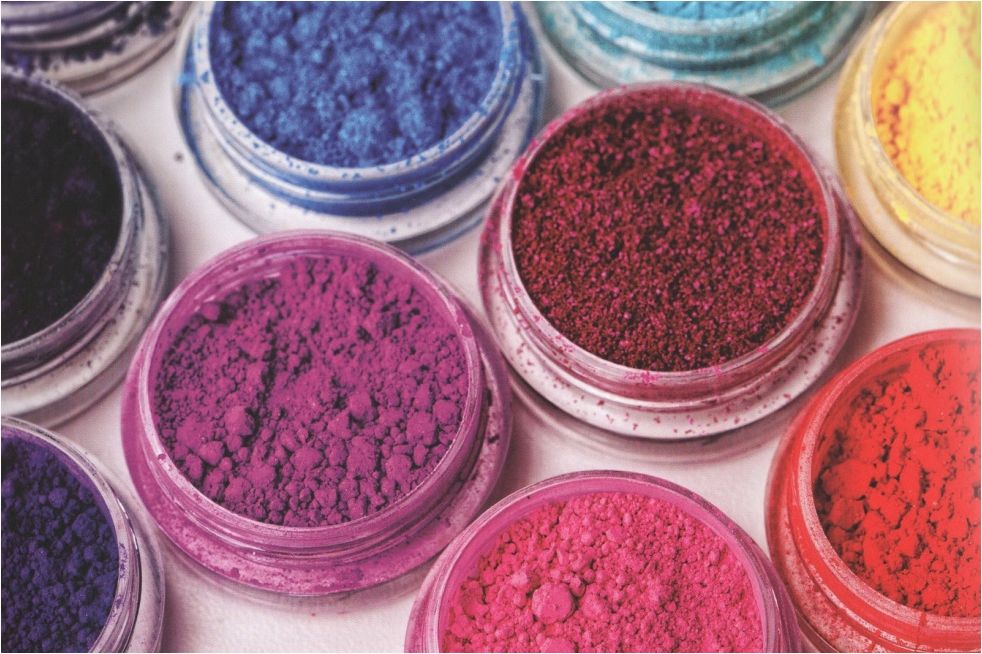
Жидкие компоненты — пластификаторы, отвердители и модификаторы обычно смешиваются с полимерами в шаровой, вибрационной или другой установке, предварительно очищенной от пигментов и наполнителей. Сухое смешивание — самый простой метод, выполняемый с помощью различных миксеров, но получаемый конечный продукт имеет менее чем однородное распределение пигментов.
Смешивание расплава осуществляется при температуре, немного превышающей температуру текучести предыдущей пленки. В то же время частицы пигмента смачивают и проникают в бывшие частицы пленки, создавая более однородную макро- и микроструктуру еще до стадии формирования пленки. Смешанные компоненты расплава возможны с любой из предыдущих пленок, но максимальное применение получили эпоксидные смолы, полиеслаты, акрилаты, олигомеры мочевой кислоты и низкомолекулярные полибороны.
Процесс изготовления включает пять операций:
- Измельчите исходные компоненты до зерен размером 1-3 микрона;
- Смешанные компоненты расплавленных полимеров или олигомеров и расплавов;
- Охлаждение расплава;
- Измельчение расплавов;
- Сухого Гереева или пороховой сепарации.
Измельчение красителя при производстве порошковых материалов происходит почти исключительно в экструдерах (шнековых смесителях). Попытки использовать другие виды оборудования себя не оправдали.
Основной частью экструдера является шнек, вращающийся в цилиндрическом корпусе. Шнек захватывает сухую смесь «предыдущая пленка — пигмент — наполнитель» из загрузочного бункера и пропускает ее через цилиндрический корпус, расплавляя и смешивая (измельчая) по мере движения. В промышленности порошковых красок используются два конкурирующих экструдера: первый — двухшнековый экструдер с двумя соединенными шнеками, вращающимися в одном направлении; второй — одношнековый, с периодически возвращающимися шнеками (S O-CALLED CO Mixer — Formulator).
Червяк двухшнекового экструдера дополнительно оснащен смесительным диском. В однокрылых экструдерах смешивание происходит из-за сложной формы и характера движения шнека в сочетании со специальными выступами на внутренней стенке цилиндра.
Основная операция — высокотемпературная смесь компонентов с температурой 90-110°C, вязкостью 10 3-10 5p.C*C в течение 0. 5-5. 0 мин в непрерывном устройстве — экструдер, двойной расширительный шнековый смеситель, четко регулируемая система нагрева. Наилучшие результаты достигаются при предварительном диспергировании пигмента в расплаве предыдущего и небольшого количества пластификатора, таким образом, что концентрат пигмента вводится в большую часть расплава предыдущей пленки вместе с остальными компонентами.
Максимальная температура расплава должна быть менее чем на 20°C выше температуры отвержденного материала, а среднее время пребывания не должно превышать время, необходимое для диспергирования.
На эффективность работы экструдера влияют:
- Эффекты сдвига (скорость, момент);
- Среднее время нахождения смеси в устройстве;
- Производительность устройства;
- Температура;
- Вязкость расплава.
Этот метод производства порошковых материалов резко улучшает дисперсию, сокращает время смешивания и снижает риск преждевременного измельчения порошка. Дисперсия частиц пигмента составляет 1-20 микрон. Этот метод производства приводит к более высоким затратам энергии на перемешивание при плавлении и последующее измельчение, но оправдывается более высоким качеством покрытий и меньшей толщиной по сравнению с методом сушки.
Недостатками этого метода производства порошковых красок являются сложность точной подгонки цветов и необходимость очистки оборудования при переходе от цвета к цвету.
Порошковые краски, полученные путем выпаривания органических растворителей из жидких красок, являются наиболее дисперсными и имеют частицы круглой формы размером 20-40 мкм. Они отличаются более высокой красящей способностью и более низкой температурой отверждения. Их производство включает в себя обычные этапы производства организованных лакокрасочных материалов, производство растворителей в сушилках сухого типа и улавливание конденсата растворителя, выделяющегося при возвращении в производственный цикл. Недостатком этого метода является его чрезвычайная взрывоопасность. Поэтому азот используется в качестве охлаждающей жидкости для сушки.
Появление порошковых материалов является естественным следствием эволюции лакокрасочной промышленности. Во-первых, материалы с высокой степенью нелетучести более экономичны в применении, а во-вторых, их широкое использование, по крайней мере, улучшает, а то и лечит экологическую ситуацию.
Все чаще используются порошковые краски, так как при окрашивании материалов образуется 100% сухой остаток. Однако их применение ограничено формой и размерами загрязненного изделия и чувствительностью подложки к выделению тепла.
Основными преимуществами порошковых красок по сравнению с традиционными органоразбавляемыми материалами являются:
- Отсутствие органических растворителей;
- Значительно меньше отходов (менее 0,05% от массы материала);
- Высокая скорость полимеризации;
- Возможность нанесения материала в один слой;
- Широкий спектр легко достигаемых спецэффектов (муар, апельсиновая корка и т.д.);
- Возможность регулировки толщины слоя покрытия;
- Почти полное отсутствие вредных выбросов;
- Низкая пожароопасность;
- Низкая стоимость покрытий.
Все порошковые краски можно разделить на две большие группы: термопластичные и термореактивные.
Технология окрашивания термопластичными порошковыми красками основана на образовании покрытия без химической реакции, которая происходит за счет слияния частиц при нагревании. Получаемые в результате покрытия термопластичны и обратимы. В основном они используются для получения функциональных покрытий — химически стойких, антикоррозионных, антизапотевающих и электроизоляционных. Покрытия обычно наносятся толстым слоем в 250 микрон и более. Типичные области их применения — защита проводов, труб, корзин посудомоечных машин, морозильных камер, шлицевых валов и узлов трения, переключателей и других изделий.
Существуют различные техники и методы нанесения порошковых материалов. Электростатический и тритостатический методы распыления. Наиболее популярные и распространенные.
Технология порошковой окраски электростатическим напылением
Популярность порошковой окраски методом электростатического напыления обусловлена следующими факторами Эффективность зарядки почти всех порошковых красок, высокая производительность порошкового окрашивания больших поверхностей, относительно низкая чувствительность к влажности окружающего воздуха, делает его пригодным для окрашивания различных порошковых и специальных эффектных материалов (металлик, шагрень, муир и т.д.). Основное оборудование для порошковой окраски.
Электростатическое распыление из пистолета.
Помимо преимуществ, электростатическое напыление имеет ряд недостатков, связанных с сильным электрическим полем между пистолетом-спреем и деталью, что может затруднить нанесение порошковых красок в углах и глубоких углублениях. Это явление известно как эффект клетки Фарадея. Этот дефект является результатом воздействия электростатических и аэродинамических сил.
Когда порошковое покрытие наносится на участок, где действует эффект клетки Фарадея, электрическое поле, создаваемое распылением, имеет максимальную напряженность вдоль края выемки. Силовые линии всегда идут к ближайшей точке и, вероятно, будут сосредоточены на краю захваченной и выдавленной области и не будут проникать дальше вглубь.
Это сильное поле ускоряет оседание частиц, образуя в этих местах толстое порошковое покрытие.
Эффект ячейки Фарадея наблюдается при нанесении порошковых красок на металлические изделия сложной конфигурации. Поэтому трудно, а в некоторых случаях даже невозможно, нанести детальное и ровное покрытие, так как внешнее электрическое поле не может проникнуть внутрь.
Помимо эффекта ячейки Фарадея, при нанесении порошковых красок в электрическом поле может возникнуть еще одна проблема. Неправильный выбор электростатических параметров в распылителе и расстояния от распылителя до детали может привести к обратной ионизации и ухудшению качество полимерных порошковых красок.
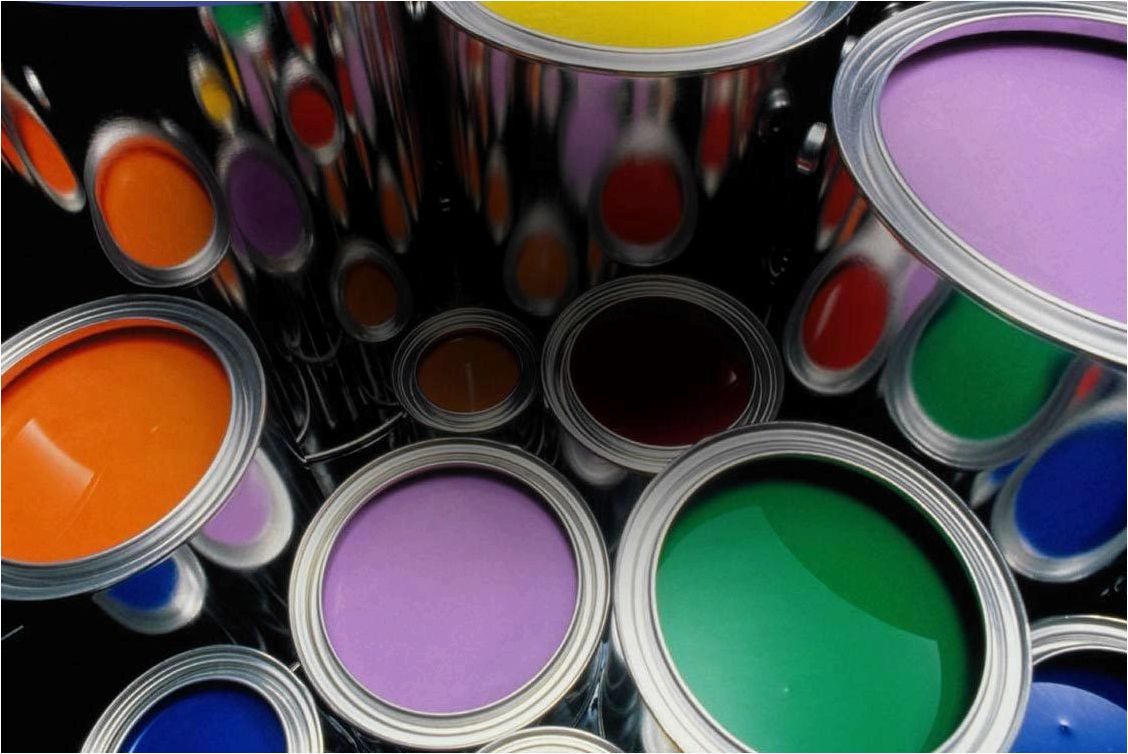
Обратная ионизация вызывается чрезмерными токами свободных ионов от зарядных электродов распылителя. Когда свободные ионы падают на поверхность детали, покрытой порошковой краской, они добавляют заряд к заряду, накопленному в слое порошка. Слишком большие заряды накапливаются на поверхности детали. В какой-то момент размер заряда настолько превышается, что микро-арт, образующий кратеры на поверхности, пропускает толщину порошка, что приводит к ухудшению качества покрытия и ухудшению его функциональных свойств. Обратная ионизация также способствует образованию дефектов «апельсиновой корки», снижает эффективность распылителя и ограничивает толщину получаемого покрытия.
Для снижения эффекта Фарадея и обратной ионизации были разработаны специальные устройства, уменьшающие количество ионов в ионизированном воздухе, так как заряженные частицы порошка притягиваются к поверхности. Заземление самого спрея позволяет свободным анионам распределяться по сторонам, значительно уменьшая проявления описанных выше негативных эффектов. Увеличивая расстояние между распылителем и поверхностью детали, можно уменьшить ток распылителя, замедляя процесс обратной ионизации.
Технология порошковой окраски трибостатическим напылением
В отличие от электростатического распыления, в этой системе нет генератора высокого напряжения для распылителя. Порошок заряжается во время трения. Основной задачей этого процесса является увеличение количества и интенсивности столкновений между частицами порошка и загруженной поверхностью пистолета-распылителя.
Одним из лучших акцепторов в линейке Triboelectric является политетрафор-этил (тефлон), который обеспечивает хорошую зарядку большинства порошковых покрытий, имеет относительно высокую стойкость к истиранию и устойчив к частицам под воздействием ударов.
Трибостатическое напыление имеет ряд существенных преимуществ:
На распылители с тритикалевым зарядом не влияют ячейки Фарадея и обратная ионизация, поскольку не создаются ни сильные электрические поля, ни ионные токи. Заряженные частицы могут проникать в глубоко скрытые отверстия и равномерно окрашивать изделия сложного состава.
- Для получения толстого порошкового покрытия можно нанести несколько слоев краски;
- Распылители, использующие тритикалевую зарядку, конструктивно более надежны, чем пистолетные распылители, заряжающиеся в поле коронного разряда, так как в них отсутствуют элементы для преобразования высоких напряжений. За исключением провода заземления, эти распылители полностью механические и чувствительны только к естественному износу.
Технология порошковой окраски в кипящем слое и струйным распылением
Технология окрашивания порошковых красок термореактивными порошковыми красками основана на том, что, в отличие от термопластичных материалов, покрытия образуются в результате химической реакции при нагревании. Такие покрытия имеют трехмерную структуру и являются нерастворимыми и нерастворимыми. Другими словами, они необратимы. Термореактивные покрытия используются для получения как функциональных покрытий, так и защитных устройств. Для достижения функциональных целей наиболее широко используются эпоксидные соединения. Они наносятся слоями по 100-150 микрон на поверхность продукта, предварительно нагретую до 50-60°C, в аппарате кипящего слоя (многократный и попеременный нагрев и погружение в порошок) или отрывистым напылением. Как правило, толщина покрытия, нанесенного этим методом, составляет от 300 до 500 микрон. Поэтому этот метод используется для покрытия изделий с небольшой площадью и сложной конфигурацией поверхностей — роторов и электродвигателей, труб (изнутри и снаружи), металлической арматуры, проводов, сеток, катушек и т.д.
Порошковые покрытия формируются одним из вышеперечисленных методов с последующей термообработкой при температуре 160-200°C в течение 10-20 минут, в течение которых порошковое покрытие плавится и растекается по поверхности изделия, образуя тонкий пласт. прочное пленочное покрытие толщиной 60-80 мкм.
В последние годы различные низкотемпературные методы (температура 120-130°C) более широко используются для нанесения покрытий на чувствительные к высоким температурам изделия. Однако низкотемпературное отверждение применимо только к эпоксидным материалам.
Отверждение покрытий с помощью ИК-излучения позволяет быстро нагреть изделие до нужной температуры, при этом значительно сокращается технический процесс и уменьшаются габариты оборудования, но этот метод отверждения подходит только для простых изделий из пенопласта. Не отбрасывайте тени на себя.
Одним из перспективных методов отверждения покрытий из порошковых материалов является УФ-проверка. Однако она не лишена недостатков. Во-первых, этим методом невозможно получить матовые покрытия; второй недостаток связан со способностью желтых пигментов поглощать свет как в УФ, так и в видимой области спектра, что делает невозможным отверждение желтых порошковых материалов.
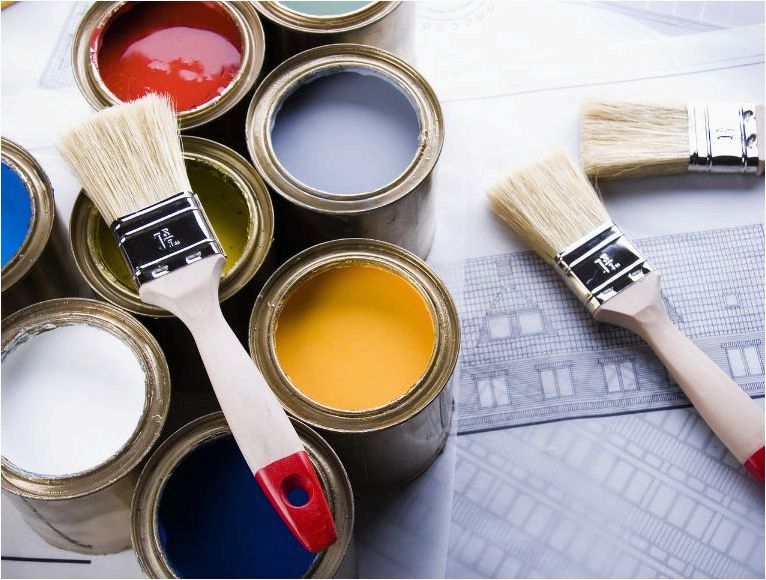
Порошковые материалы в основном используются для нанесения покрытий на металлы. Однако более новые технологии и оборудование для порошковой окраски могут использоваться для покрытия других материалов, таких как стекло, керамика и штамповки MDF (средневолокнистые текстильные плиты).
Хотя порошковая технология имеет много преимуществ, существуют некоторые ограничения в производстве тонких, гладких декоративных покрытий. Текстура и свойства поверхности зависят от типа порошкового покрытия и настроек оборудования для технологии порошковой окраски. Для получения высококачественных порошковых красок очень важно соблюдать технологию нанесения и температурный режим.
Многие производители предпочитают наносить порошковые краски с эффектом «апельсиновой корки». Это позволяет скрыть дефекты металла, возникающие в процессе производства.
Порошковые краски также имеют важное преимущество: не оседающую краску можно собирать и использовать повторно. Однако, если в цветовом цикле используется несколько цветов, это накладывает определенные ограничения на вторичное использование материала. Такие порошковые краски, отвечающие всем требованиям нормативных документов, за исключением показателя «цвет цвета», называются «вторичными». Как правило, она используется для детальной покраски, и ее декоративные свойства не имеют принципиального значения.
Использование порошковой краски и лака предполагает получение прочного покрытия. Однако если порошковую краску необходимо удалить, для этого существуют специальные средства.
Порошковая технология не является сложной, но требует практических навыков и опыта работы.